What is warehousing and inventory management
Elevating Logistics: Seamlessly Handling Goods and Efficiently Managing Physical Inventory for Sales and Distribution.
Effectively oversee warehouses and products prior to shipment or use in manufacturing. Streamlined warehousing guarantees timely delivery to customers or manufacturing, minimizing errors, and preventing lost or stolen fulfillment orders. The warehousing process encompasses receiving, putaway, picking, packing, and shipping.
Warehouse Management
Manage one - or a hundred warehouses inclusive their inventory.Inventory Management
Manage Stock Quantities, variations and inventory pricing.Receiving and Delivery
Add and deduct stock from warehouses, adjust and record loss.“ The easiest and fastest ERP I worked with. Fabulous support and excellent data integrations. Using it for all of my companies and I have to say.. I am truly satisfied. ”

Benjamin "Ben" Talin
CEO | MoreThanDigitalInventory and Warehousing features for faster logistics and stock management
Manage your warehouse and inventory with full integration into your sales and management processes
Following leading industry standards
Manage your warehouses and logistics at ease
The warehousing feature allows you to easily manage your inventory, vendors, and warehouses in a single dashboard. Integrated with sales, proposals, and ecommerce, you can automate the information flow of all your goods within the commodity list. The WMS gives complete control following leading industry standards for integration.
- Integrate easily with your vendors
- Following leading industry standards
- Full integration with all SIX sales modules
Manage multiple warehouses and their inventory
Don’t limit yourself from growth
The system allows you to manage multiple different warehouses. Quickly transfer goods from one warehouse to another, manage stock, loss and even track the history of every good. The warehousing software gives you unlimited scalability of your business and total control over the flow of commodities.
- Manage unlimited warehouses
- Transfer goods between warehouses
- Full stock management for every warehouse
Full traceability of commodities and inventory
Get insights into your whole flow of goods
Don’t just manage the flow of goods within your own company. With the full interoperability using APIs, you can access information from outside the company, integrate it into the process and connect your warehouse management system with other 3rd party systems at ease.
- Integrate with external systems via API
- Get transparency into your flow of goods
- Consistent data management
Manage all aspects of your inventory
Stock management, product management, and more
Manage important information around your goods and inventory. Manage minimum and maximum stocks, define pricing, markups, and product features. The inventory system gives you complete control of every aspect of your products.
- Manage product details
- Stock Management
- Inventory Control and Management
Seamless, Smart, and Stress-Free – Welcome to SIX ERP.
The WMS leading companies trust
Tap into a global network of companies who already know and trust SIX.
managed by SIX
Use SIX to manage inventory and stock
use SIX to drive business and growth
We are not SaaS - You own your data!
Own your Product data
You have your own decoupled pods with all your data. You decide who can access product-related data. You own your data - always!
European solution
Trusted solution built with the strict European standards in mind. SIX is built for leading global companies.
GDPR compliant
Be on the safe side when it comes to data compliance. Our GDPR module makes it possible to manage all data without any hassles safely.
Interesting Blog Articles
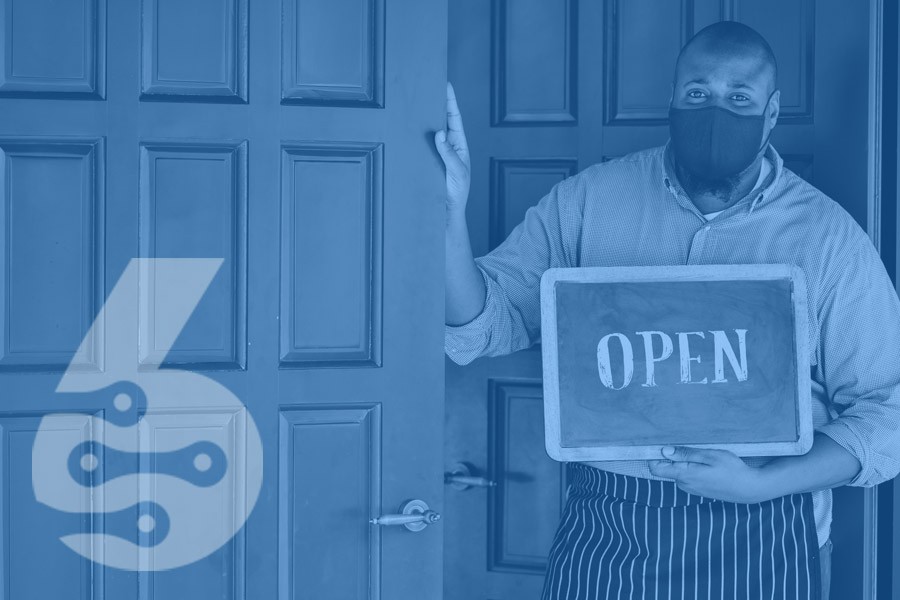
10 key features SMEs should look for in a modern ERP software
SMEs are the backbone of the economy. SMEs account for 99.7% of businesses in regions like Europe and the U.S. and employ over 60% of the workforce. But even though they're critical to economic growth, SMEs often struggle to manage even the most basic tasks, like finances, customer data, inventory,...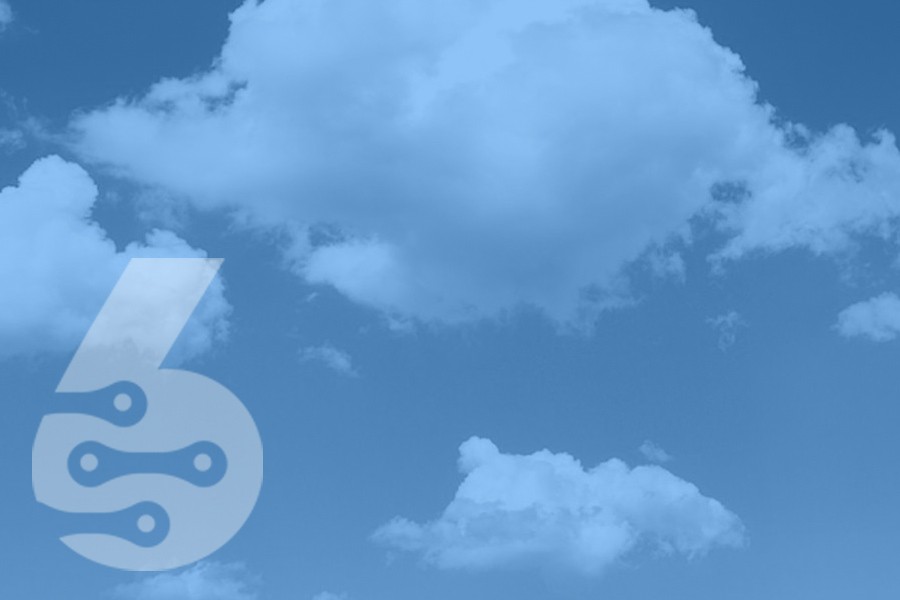
Managed Cloud ERP
As your business grows, it becomes increasingly important to have a reliable and efficient system to manage your operations. A cloud-based ERP system is the perfect solution for businesses of all sizes, from small SMEs to large global corporations. Not only is it scalable, but it also provides several other...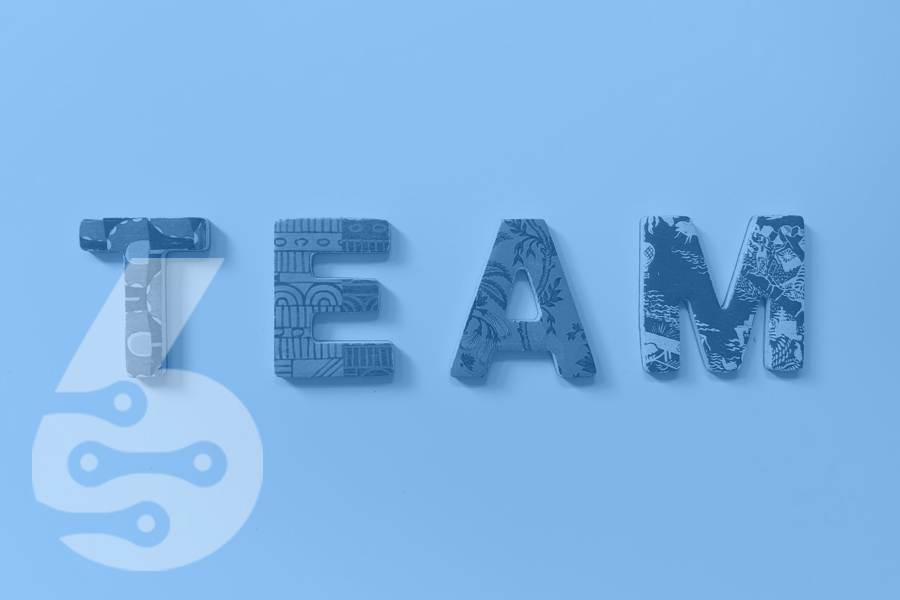
ERP implementation team structure
ERP (Enterprise Resource Planning) systems are essential for businesses of all sizes to streamline operations and increase efficiency. ERP software integrates different business processes, such as accounting, human resources, inventory control, and customer relationship management. The right team structure is critical when implementing an ERP system to ensure the implementation...Want to learn more about Warehouse Management?
How to choose the best Warehouse Management Solution (WMS)?
Choosing the right Warehouse Management Solution (WMS) is vital to streamline your warehouse operations and increase overall productivity. There are 3 key factors you should consider when making the decision between the right WMS systems:
- Understand your warehouse needs: Before embarking on the selection of a WMS, you must have a clear understanding of your warehouse operations. This includes knowing your inventory levels, order volume, the complexity of your operations, your growth forecasts and your specific pain points. This step will help you identify the functionality you need in a WMS. Also understand what you want to optimize or where you can increase your efficiency. Often you need to rethink the warehouse management completely.
- Evaluate the different WMS offerings: Once you know what you need, it's time to evaluate the different WMS options available on the market. Look for solutions that cater to companies similar to yours in terms of size and industry. Consider their features, scalability, integration capabilities and customer services.
- Determine the scalability of the solution: The WMS you choose should be able to grow with your business. As your operations expand, the software must be able to accommodate larger inventory, additional users and more complex functionality. Make sure you choose a WMS that fits your long-term business goals.
Remember, the best WMS for your company will be the one that meets your specific needs and can easily adapt as your business evolves. Don't necessarily look for solutions that offer hundreds of features you might not need and pay a premium for unused features. Try to also find WMS solutions that integrate easily with your company or are integrated with ERP systems.
Advantages of Warehouse Management Solutions
Implementing a warehouse management solution (WMS) can offer numerous benefits to your company. Here are some key benefits which most companies will experience after they implement a WMS solution:
- Inventory tracking and management: WMS provides real-time tracking of inventory, which minimizes the risk of overstocking or out-of-stocks. This can significantly reduce costs related to excess inventory and prevent lost sales due to out-of-stocks.
- Streamlining warehouse operations: A WMS can streamline your warehouse operations by automating various tasks, such as order picking, packing and shipping. This reduces manual effort and increases efficiency. In addition, a well-implemented WMS can help optimize warehouse layout and improve employee productivity.
- Improved efficiency and productivity: By automating routine tasks, reducing errors and optimizing workflows, a WMS can significantly improve the efficiency and productivity of your warehouse. Faster order fulfillment can also improve customer satisfaction.
- Error reduction and risk mitigation: A WMS helps minimize errors in order processing and inventory management, resulting in fewer customer complaints and returns. In addition, by providing complete visibility into your warehouse operations, a WMS can help identify potential problems before they become major issues.
What is the difference between WMS and Supply Chain Management System?
Both Warehouse Management Systems (WMS) and Supply Chain Management Systems (SCM) play key roles in managing a company's operations. However, they have different objectives and unique functionalities.
Definition of WMS and SCM
A Warehouse Management System (WMS) is primarily focused on controlling the movement and storage of materials within a warehouse and processing the associated transactions, including shipping, receiving, picking and putaway. In contrast, a Supply Chain Management System (SCM) system is more comprehensive. It manages the entire supply chain process, from raw material procurement to product distribution, transportation management, inventory control, order fulfilment and customer service.
Understand the key features of each
A WMS offers functions such as inventory tracking, warehouse layout optimization and labour management to streamline warehouse operations. SCM systems, meanwhile, offer functionality such as demand forecasting, production scheduling, order processing and transportation management, allowing companies to monitor and manage their entire supply chain more effectively.
Where they overlap and how they differ
While there is some overlap, primarily in inventory management and order processing, the main difference lies in their scope. A WMS focuses specifically on optimizing warehouse operations, while an SCM system has a broader scope, encompassing all aspects of the supply chain.
Why WMS should be integrated with Supply Chain Management Systems
Integrating Warehouse Management Systems (WMS) with Supply Chain Management Systems (SCM) can bring considerable benefits to a company. Here's why:
- Streamlining operations: By integrating WMS with SCM, you can automate and streamline the entire process, from inventory acquisition to product delivery. This results in faster, more efficient operations and less manual intervention, reducing the risk of errors.
- Improved data visibility: Integration provides complete, real-time visibility into your entire supply chain. From tracking inventory levels in your warehouse to monitoring the status of deliveries, you'll have access to critical data at every step. This allows you to make better decisions and improve forecasting.
- Increase overall supply chain efficiency: With integrated systems, you can optimize all aspects of your supply chain, from warehouse operations to transportation logistics. This can help reduce costs, improve customer service and increase profitability.
Most commonly used WMS functionalities
A Warehouse Management System (WMS) offers a multitude of features designed to streamline and improve your warehouse operations. Here are some of the most commonly used features:
- Inventory control: the WMS provides real-time tracking and management of your inventory. It can monitor stock levels, manage SKUs, track product locations and provide alerts when inventory is low or high, enabling effective inventory control.
- Order fulfilment: The WMS can automate the entire order fulfilment process, including picking, packing and shipping. It ensures that orders are processed quickly and accurately, improving customer satisfaction.
- Batch picking: WMS systems often offer batch picking capabilities, which allow warehouse personnel to pick multiple orders simultaneously. This can significantly improve picking efficiency and reduce the time required to fulfil orders.
- Shipping and receiving tracking: The WMS can monitor the entire shipping and receiving process, providing real-time updates on the status of shipments. This can help you manage logistics more efficiently and ensure on-time delivery of products.
- Optimizing warehouse space and layout: The WMS can help you design and manage your warehouse layout to make the best use of space. It can determine optimal locations for products based on factors such as size, weight and frequency of access, improving efficiency and productivity.
- Real-time reporting and analysis: WMSs can provide real-time information and analysis on warehouse operations. This can include data on inventory turns, order fulfilment times, employee performance and more. This information can help you make data-driven decisions to optimize your operations.
- Barcode and RFID scanning: These capabilities allow you to enter and retrieve data quickly and accurately, reducing manual errors and streamlining various warehouse processes, such as receiving, order picking and stock counting.
- Integration with other systems: WMS solutions can often integrate with other enterprise systems, such as ERP (Enterprise Resource Planning) and SCM (Supply Chain Management) systems. This integration can help create a seamless flow of information between different parts of your business, improving overall operational efficiency.
How to use WMS for inventory management
Inventory management is an important aspect of warehouse operations for every company that needs to actively manage stock, products or order fulfillment, and a warehouse management system (WMS) can greatly simplify the process. Here's how:
- Track inventory levels: with a WMS, you can track your inventory levels in real time. It provides detailed information about what items are in stock, what quantities they contain, and where they are in the warehouse. This visibility can help avoid overstocking and understocking.
- Demand forecasting: some advanced WMS solutions are equipped with predictive analytics capabilities that can forecast future demand based on historical data. This allows you to plan your inventory more accurately and efficiently, ensuring that you always have the right amount of goods in stock.
- Reduce overstocking and out-of-stock situations: With real-time tracking and demand forecasting, a WMS can alert you when inventory levels are too low or too high. That way, you can prevent out-of-stock situations that can lead to lost sales, and overstocks that tie up capital and warehouse space.
- Reorder point automation: WMSs can automate the reorder process by setting up reorder points. When inventory levels fall below a certain point, the system can automatically trigger an order, ensuring you never run out of important items.
Common challenges in a WMS implementation
Implementing a warehouse management system (WMS) can bring many benefits, but it is also a complex process that can present some challenges for businesses. Here are some common issues that usually arise when implementing a WMS:
Managing change
Implementing a new system often requires significant changes to processes and workflows. This can be disruptive and met with resistance from employees. It is important to manage this change effectively through clear communication, employee training and a phased rollout. Often manual processes are automated and this can also cause a lot of resistance internally.
System integration issues
A WMS must work seamlessly with other systems such as ERP and SCM systems. Systems like SIX ERP are already integrated. However, if the systems are separate, integration can sometimes be a complicated process, especially if the other systems are outdated or from different vendors and not designed to communicate with each other.
Employee training and adoption
The success of a WMS implementation depends heavily on how well your employees can use the system. Proper training is important, but can be time-consuming and difficult, especially if the system is complex.
Data migration
Transferring data from your old system (or no system) to the new WMS can be a daunting task. It is important to ensure that the data is accurate and complete to avoid problems later. Images should also be properly deposited and processes implemented to ensure data quality is correct.
Customization issues
While most WMS solutions can be customized to meet the unique needs of the organization, customization can be a complex process that requires technical expertise, and it often results in cost explosion because the complexity is usually difficult to estimate.
Resolving the Challenges
All of these challenges are predictable but require thorough planning, ongoing communication, staff training and good project management. Working with a reputable WMS vendor who can provide technical support and advice can also be invaluable. For 95% of companies, it pays to go with an ERP that has warehouse management built in, which results in much lower costs and is often faster and smoother during integration. Complex stand-alone WMS systems are usually only necessary in special cases.
Why should you work with a WMS?
A warehouse management system (WMS) can bring numerous benefits to your business. Here are the reasons why you should consider implementing a WMS:
- Improved inventory control: by tracking inventory in real time, a WMS can help maintain optimal inventory levels and reduce the risk of overstocking or understocking.
- Improved operational efficiency: a WMS automates various warehouse processes, reduces manual errors, optimizes space and resource utilization, and improves the overall efficiency of your warehouse operation.
- Cost savings: By optimizing inventory, reducing waste, improving labor productivity, and speeding up order fulfillment, a WMS can result in significant cost savings.
- Better customer service: faster and more accurate order fulfillment leads to higher customer satisfaction. A WMS can provide real-time information about inventory and shipping status, so you can better serve your customers.
- Data-driven decision making: With the real-time data and analytics that a WMS provides, you can make informed decisions to improve your warehouse operations.
- Scalability: A WMS can grow with your business and adapt to larger inventories, additional users, and more complex operations. This makes it a long-term solution for your warehouse management needs.
- Shorter turnaround times: Through streamlined operations and optimized workflows, a WMS can shorten lead times for order fulfillment and help you better meet your customers' expectations.
- Higher accuracy: By automating various warehouse operations and eliminating manual tasks, a WMS can significantly increase the accuracy of processes like picking, packing and shipping.
- Better supplier relationships: With improved inventory management, you can better manage your ordering process and maintain healthier relationships with your suppliers.
- Better workforce management: A WMS can provide insight into employee productivity and help manage labor resources more effectively, resulting in higher productivity and lower labor costs.
- Increased security: A WMS often includes security features to protect your warehouse operations, inventory and data. This can include user access controls, audit trails and data security measures.
- Compliance management: Some WMS solutions offer features that help with regulatory compliance by providing reporting capabilities and ensuring that warehouse operations adhere to relevant standards and regulations.
SaaS, Cloud, Managed Cloud or On-Premise WMS.
When it comes to implementing a warehouse management system (WMS), you have several options: Software-as-a-Service (SaaS), Cloud, Managed Cloud or On-Premise. Here's a brief overview of each option:
- SaaS WMS: This is a web-based model where you access the WMS over the internet. You pay a subscription fee, usually monthly or annually, which includes the cost of software updates and maintenance. This model lowers initial costs and is quick to get up and running, but is quite expensive in the long run, as recurring costs add up significantly.
- Cloud WMS: Similar to SaaS, a cloud WMS is hosted on a cloud server rather than on your own servers. It offers the same benefits as a SaaS WMS, with the added flexibility to scale up or down resources as needed, but lower costs compared to SaaS models because you're not paying per employee, per warehouse, or other models.
- Managed Cloud WMS: In this model, the WMS provider not only hosts the application in the cloud, but also manages all aspects of the solution, including maintenance, updates and support. This allows you to focus on your core business instead of worrying about IT management. SIX ERP is an example of how you don't have to worry about anything other than using the software. This model offers some of the lowest operating costs and maintenance costs compared to other solutions.
- On-Premise WMS: Here, the WMS software is installed and operated on servers in your own facility. This option requires a higher initial investment and maintenance, but gives you more control over your data and is more customizable. This option is usually a good choice if you have a large in-house IT team or you have special compliance requirements but is unnecessarily expensive and complicated to maintain for 95% of businesses.
Each of these deployment options has its own advantages and disadvantages, and the best choice will depend on your specific needs, budget and IT capabilities. For most small and medium-sized businesses, however, a cloud-hosted or, more importantly, a managed cloud solution offers the best value for money.
WMS Reports and Analyses
Reporting and analysis functions are important components of a warehouse management system (WMS). They give you insight into your warehouse operations and allow you to make informed decisions and improve efficiency. Here's a brief overview of what WMS reports and analytics can provide:
- Real-time visibility: WMS can provide real-time data on your warehouse operations, such as inventory levels, order status, and warehouse performance. This allows you to monitor your operations in real time and quickly identify and fix any issues.
- Performance tracking: With WMS, you can track various performance metrics, such as order fulfillment times, picking accuracy, and employee productivity. With this data, you can identify areas for improvement and measure the impact of the changes you make.
- Forecasting: Some WMS solutions have advanced analytics that allow you to forecast future demand based on historical data. This helps you better plan your inventory levels and avoid over- or understocking.
- Trend analysis: WMSs can analyze your data over time to identify trends in your warehouse operations. This gives you valuable insight into seasonal fluctuations in demand, changes in supplier performance, and the impact of changes in your operation.
- Custom reports: Most WMS solutions allow you to create custom reports tailored to your specific needs. This allows you to focus on the data that matters most to your business.
How do I choose the best WMS for me?
Choosing the right warehouse management system (WMS) can be a difficult task, given the many options on the market. Here are some factors to consider when choosing a WMS for your business:
- Your specific needs: Which WMS is best for you depends on your unique business needs. These include the size and complexity of your warehouse, the number of users, the volume of transactions, and the specific features you need.
- Integration capabilities: Your WMS should integrate seamlessly with your other business systems such as ERP, CRM and SCM. This will ensure a smooth flow of data between the different systems, increasing efficiency and reducing the risk of errors. Best would be a solution that is already integrated in an ERP that combines ERP, SCM and CRM like SIX ERP.
- Ease of use: A user-friendly WMS is easier for your staff to learn and use, leading to faster adoption and fewer errors.
- Vendor reputation: It is important to choose a vendor that has a good reputation in the market. Pay attention to factors such as its experience in the industry, customer reviews, and customer service.
- Budget: the cost of WMS solutions can vary widely. Consider not only the initial cost of the software, but also ongoing costs such as maintenance, updates and training.
- Customization options: Every business has its own needs and processes. It's important that you choose a WMS that can be customized to meet your specific needs.
- Security features: Since your WMS deals with sensitive data, it's important to choose a system with robust security features. These include data encryption, user access control and audit trails.
- Compliance management: If your industry is subject to certain regulations, you may need a WMS that offers compliance features. This might include reporting capabilities and the ability to enforce certain procedures.
- Scalability: As your business grows, your WMS should be able to grow with it. A scalable WMS allows you to add more users, process larger volumes of transactions and add new features as needed.
Hundreds of leading companies trust SIX
Want to see SIX for yourself?
Need help, have questions or want to get a free demo?
Please read our Privacy Policy on how we process personal data. We will never share your data!