- Manufacturing
- 02.04.2025
Fresh, Fast & Future-Proof: The Smart Way to Produce Dairy
Revolutionizing Dairy Production: Efficiency, Quality, and Innovation Through Smart ERP Integration
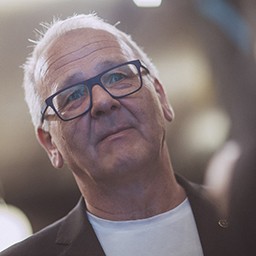
Dr. Andreas Maier
02.04.2025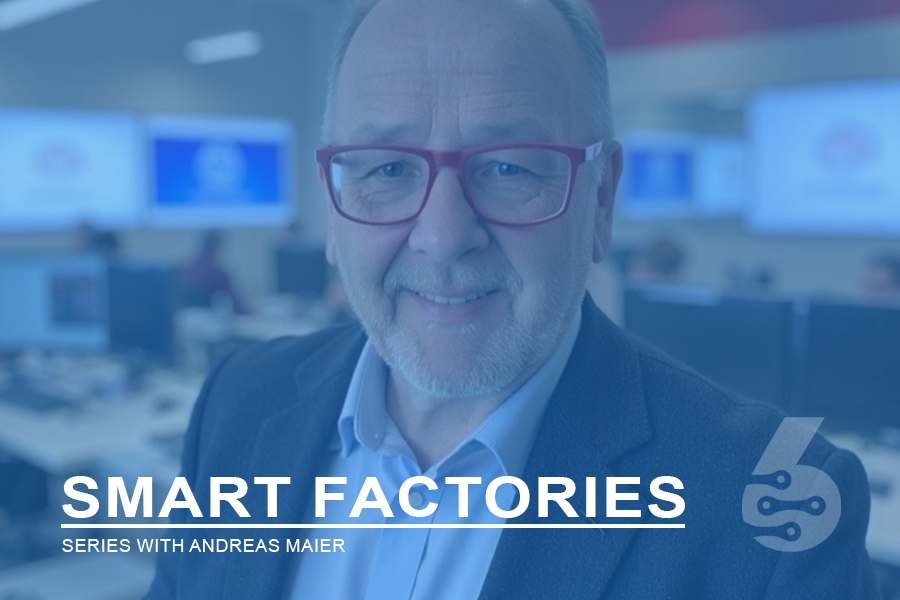
“ Just as every drop of milk matters in the production cycle, every data point in a smart factory shapes the future of dairy manufacturing - where precision and innovation meet consistency and quality. “
Milk production is one of the most demanding sectors in food manufacturing, where quality, consistency, and safety are non-negotiable. Unlike other industries, dairy processing requires precise control over every stage - from raw milk intake to packaging - to maintain strict hygiene standards and ensure uniform product quality. This level of precision is only possible through advanced automation and data-driven decision-making. That’s where SIX ERP comes in. By integrating real-time monitoring, automated workflows, and predictive analytics, our ERP system transforms dairy factories into intelligent, self-optimizing facilities.
In this article, I’ll take you through the milk production cycle from a factory’s perspective, highlighting how modern a modern ERP solution, coupled with cutting-edge machinery and sensor technology, ensure high-quality milk output at scale.
From Farm to Factory: The Journey of Raw Milk
The milk production cycle begins long before the factory floor - it starts at the dairy farms, where raw milk is collected, tested, and transported under strict temperature-controlled conditions. Upon milk arrival at the processing facility, ERP systems take over, integrating data from sensors that measure temperature, pH levels, fat content, and potential contaminants in real time. Automated quality control mechanisms ensure that only milk meeting predefined standards enters production. This seamless integration of ERP with laboratory testing and logistics not only reduces human error but also enables immediate corrective actions, ensuring that every batch starts with the highest possible quality.
Precision Processing: Automation and Real-Time Monitoring
Modern dairy factories rely on high-tech pasteurization, homogenization, and separation systems - all tightly integrated with the ERP to ensure optimal efficiency.
Temperature-sensitive processes like pasteurization require real-time monitoring, with sensors continuously feeding data to the ERP to adjust heating cycles dynamically. Too little heat, and harmful bacteria remain; too much, and the milk’s nutritional value degrades. Homogenization, which ensures a uniform texture and prevents cream separation, is similarly controlled through automated flow adjustments, maintaining consistency across thousands of liters. By centralizing this data, the ERP enables factory managers to oversee the entire process remotely, ensuring that production adheres to both regulatory requirements and internal quality standards.
SIX ERP – The Operating System for Your Business Reality.
Packaging and Distribution: Ensuring Quality Beyond the Factory
Once the milk is processed and standardized, it moves to the packaging stage - an area where precision and hygiene are paramount. Automated filling machines, integrated with SIX ERP-controlled workflows, ensure that every container is filled to exact specifications, sealed properly, and labeled with traceable batch information. Sensors monitor packaging speed, fill levels, and temperature to prevent inconsistencies or contamination risks.
Beyond packaging, SIX ERP plays a crucial role in managing the cold chain logistics required for milk distribution. RFID tags and IoT-enabled tracking devices provide real-time updates on storage conditions, ensuring that milk remains within the required temperature range from the factory to retail shelves. Route optimization algorithms help streamline distribution, minimizing transit times and reducing the risk of spoilage. By connecting the entire supply chain, we maintain quality, reduce waste, and ensure that consumers receive fresh, high-quality milk every time.
Compliance and Sustainability: Meeting Industry Standards and Reducing Environmental Impact
Milk production is heavily regulated to ensure consumer safety and product integrity. From pasteurization records to microbial testing, every aspect of production must comply with strict food safety regulations such as HACCP, ISO 22000, and local dairy standards. SIX ERP integration simplifies compliance by automating data collection and generating real-time reports that auditors and regulators can access instantly. Every batch of milk is tracked from raw collection to final distribution, ensuring full traceability in case of quality concerns or recalls.
Sustainability is also a growing focus in dairy production, where energy consumption, water usage, and waste management must be optimized.
Throughout the entire process we monitor energy efficiency across the factory, ensuring that pasteurization and refrigeration units operate at peak efficiency. Automated cleaning-in-place (CIP) systems reduce water consumption while maintaining hygiene standards. Additionally, predictive analytics help optimize raw material usage, reducing excess milk waste and improving overall resource efficiency.
By integrating compliance and sustainability measures directly into factory operations, we not only ensures regulatory adherence but also drive long-term efficiency and environmental responsibility.
Challenges in Implementing SIX ERP in a High-Tech Dairy Production Facility
Implementing an ERP system in a highly technical dairy production facility presents unique challenges that go beyond standard software integration. Unlike traditional manufacturing, where processes are often linear and predictable, dairy production involves complex, interdependent workflows that require real-time monitoring and precision control. One of the biggest hurdles we faced was integrating with the existing machinery and sensor networks, ensuring seamless data exchange without disrupting production.
For example, during one implementation, we encountered discrepancies in real-time temperature readings from pasteurization units. While the ERP system relied on direct data input from industrial sensors, slight calibration differences caused inconsistencies in recorded temperatures. This led to alarms being triggered unnecessarily, disrupting workflow efficiency. To resolve this, we worked closely with factory engineers to fine-tune sensor calibrations and establish better data filtering mechanisms within the ERP system, ensuring only relevant deviations triggered corrective actions.
Another challenge was aligning the ERP with the plant’s automation systems. Many dairy factories operate with programmable logic controllers (PLCs) that manage key processes such as milk separation, homogenization, and sterilization. The difficulty was ensuring that ERP commands and process data were synchronized with PLC workflows without causing bottlenecks. Through iterative testing and API customizations, we successfully enabled real-time ERP-PLC communication, allowing for automated process adjustments based on live production data.
These challenges highlighted the need for deep technical expertise and a hands-on approach. ERP implementation in dairy production isn’t just about installing software - it’s about ensuring that every machine, sensor, and system works together to create a unified, intelligent production environment.
Testing and Simulation Before Implementation: A Smart-First Approach
Before deploying an ERP system in a high-tech dairy production facility, we apply the same test and simulation philosophy that proved invaluable in other production implementations. Rather than diving straight into live operations, we create a digital twin of the entire production process - mapping every stage from raw milk intake to pasteurization, homogenization, and packaging. Using routing workflows, and sensor data modeling, we simulate production cycles to identify inefficiencies, bottlenecks, and potential integration challenges before they occur on the factory floor.
This approach is not just theoretical - it’s a stress test for reality. During our work with similar manufacturing processes, digital simulations helped us fine-tune production parameters before a single product was produced.
We applied the same principles in dairy processing by simulating pasteurization temperatures, storage conditions, and cleaning-in-place (CIP) cycles to ensure optimal efficiency. By analyzing factors like processing time, machine workloads, and ingredient consumption, we ensure that the ERP system is optimized before real-world execution.
By the time we move to physical implementation, we already have a data-driven, well-calibrated production model - reducing downtime, preventing costly errors, and ensuring that every sensor and machine works in harmony with the ERP from day one.
Real-Time Monitoring and Automated Adjustments
Once the ERP system is live, real-time monitoring becomes the backbone of a smart dairy production facility. Unlike traditional systems that rely on periodic manual checks, SIX ERP integrates with IoT sensors, SCADA systems, and PLC controllers to provide continuous data flow across the entire production line. Every stage - from raw milk reception and pasteurization to fermentation, homogenization, and bottling - is tracked with precision.
For instance, temperature sensors ensure pasteurization is consistently maintained at optimal levels, preventing bacterial contamination while minimizing energy waste. Flow meters and pressure sensors monitor liquid movement across pipelines, ensuring that CIP (Cleaning-in-Place) systems run effectively without excessive water or chemical usage. Any deviation from set parameters triggers automated corrective actions, such as adjusting temperature settings, modifying production speeds, or alerting operators to take preemptive action.
By combining real-time analytics with automated control loops, we enable predictive maintenance, reduce production variability, and ensure each batch of milk meets strict quality standards. This integration doesn’t just monitor production - it actively enhances it, allowing the factory to adapt to changing raw material conditions, fluctuating demand, and regulatory requirements without compromising efficiency.
Integration and Collaboration with Production Teams
A critical part of our ERP implementation is the close collaboration between the technical team and the production operators. While the technology provides the foundation for automation and data-driven decision-making, the human element ensures that the system is aligned with the practical realities of the factory floor. By involving operators early in the process, we gain valuable insights into how the system can best serve their needs while also addressing challenges unique to their daily workflows.
For example, during the implementation phase, we worked alongside the factory’s operators to fine-tune sensor feedback and optimize process flows based on real-world feedback. This allowed us to adjust the system’s settings for things like milk viscosity and fat content - parameters that are essential for maintaining consistency in products like yogurt and cream.
Moreover, cross-department collaboration was key during the integration of supply chain data with production insights. By incorporating inventory and raw material management into the ERP system, we were able to streamline the entire milk production cycle, from the dairy farm to packaging. Real-time inventory tracking ensures that raw milk is received, stored, and used optimally, preventing both shortages and overstocking.
As we continue to integrate ERP into the system, the feedback from operators allows us to adjust automation thresholds, adapt to any production challenges, and fine-tune the system’s effectiveness. This approach ensures that every update is relevant and maintains high levels of engagement between technology and operators, empowering them to make smarter, faster decisions.
Results and Benefits for the Dairy Production Facility
Once the ERP system was fully integrated into the milk production facility, the improvements were immediately visible. Production efficiency saw a significant boost as processes were streamlined, allowing for faster throughput and more reliable operations. With automated scheduling, raw material handling became more efficient, and we minimized human error, which is often the culprit behind costly mistakes or delays.
But the real impact came in quality control. The system’s ability to monitor and track each step in real-time meant that any fluctuation in milk quality - whether in the pasteurization process, during homogenization, or packaging - was immediately flagged. This allowed us to take corrective actions before a batch of milk became subpar, ensuring consistent quality throughout the production process. The system also enabled better tracking of product batches, ensuring that traceability and compliance with food safety regulations were always maintained.
Beyond operational improvements, SIX ERP empowered the facility with advanced analytics, which enabled data-driven decision-making. By analyzing past performance data, we could predict potential bottlenecks or downtime, which helped us to optimize production schedules and prevent interruptions. This predictive capability was instrumental in keeping costs under control and ensuring that production runs smoothly without the need for constant manual oversight.
Ultimately, the benefits were not just operational. With enhanced visibility across the supply chain and real-time insights into production, the client now had a powerful tool for better demand forecasting, inventory management, and logistics planning. This provided them with the flexibility to scale production while maintaining consistent product quality and improving customer satisfaction. Our solution didn’t just automate the facility; it created a smart, data-driven environment where everything from milk quality to energy consumption was actively optimized.
Benefits for the Client
For the client, the integration of SIX ERP transformed not just the efficiency of their operations but also their long-term growth potential. With the system in place, they gained a real-time view of every aspect of the production process - from raw material intake to the final product leaving the facility. This level of transparency allowed for better decision-making, empowering managers to proactively address issues before they became problems.
The enhanced predictive capabilities of the ERP system meant that production schedules could be optimized, energy consumption minimized, and maintenance cycles better planned. This resulted in cost savings across multiple areas of the business, from labor to energy. Additionally, the improved quality control allowed the facility to maintain the highest standards while minimizing waste, ensuring that only the best-quality milk reached the market.
The scalability of SIX ERP was a key advantage. With an infrastructure in place that could grow with the company, the client now has the flexibility to expand production, adapt to changing market demands, and even introduce new product lines with minimal disruption. This was crucial for maintaining their competitive edge in an industry where consumer preferences and market conditions can shift rapidly.
Ultimately, the client now operates a smarter, more responsive factory. They’re better equipped to handle fluctuations in production, manage their supply chain with precision, and meet the demands of the modern dairy market. SIX ERP has proven to be a critical enabler for their continued growth and success.
Are you facing challenges in your business that you're trying to solve?
Let’s connect for a FREE 30-minute consultation call and see how I can help you move forward.
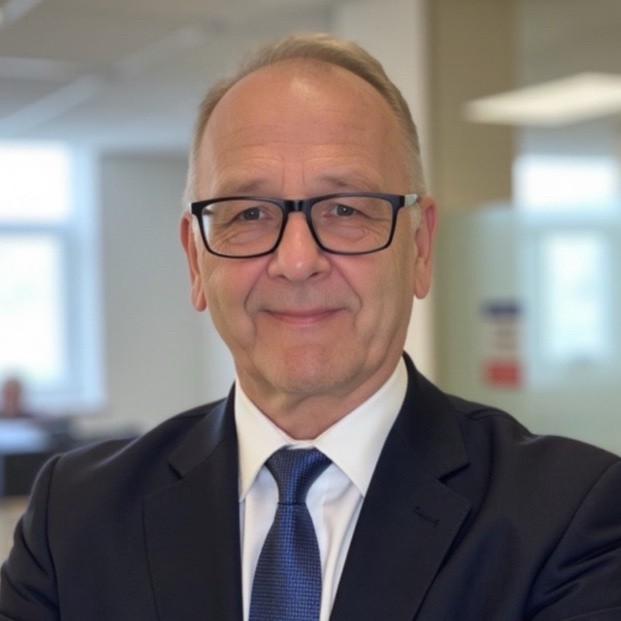
Let's Solve Your Unique Manufacturing Challenges Together
If you’re facing complex challenges in your manufacturing processes and looking for a solution that not only enhances efficiency but also drives innovation, we’re here to help. Whether you’re dealing with intricate machinery, varying production demands, or the need for real-time insights, we specialize in creating tailored ERP solutions that integrate seamlessly into your existing systems. Let’s work together to optimize your production lines, improve quality, and future-proof your operations. Reach out to us today, and we’ll show you how our smart, scalable solutions can transform your manufacturing processes and set your business on a path to long-term success.
About the author
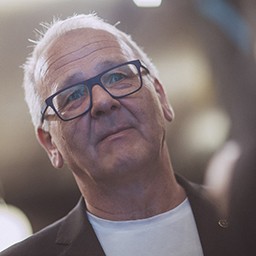
Andreas Maier is a results-driven CEO with nearly 30 years of experience in ERP, digital transformation, and IT consulting. He has held leadership positions in Fortune 100 companies such as rentalcars.com (PCLN) and Intrasoft International, a leading EU-based R&D software vendor. With a Ph.D. in Neural Networks from the University of Cologne, Andreas combines deep technical expertise with a strategic approach to business process optimization.
As the founder and co-founder of multiple successful startups, including XXL Cloud Inc., eShopLeasing Ltd, and WDS Consulting SA, his expertise lies in ERP consulting, IT strategy, and process automation. His work is focused on helping businesses implement scalable ERP solutions, streamline operations, and drive digital transformation.
Related articles
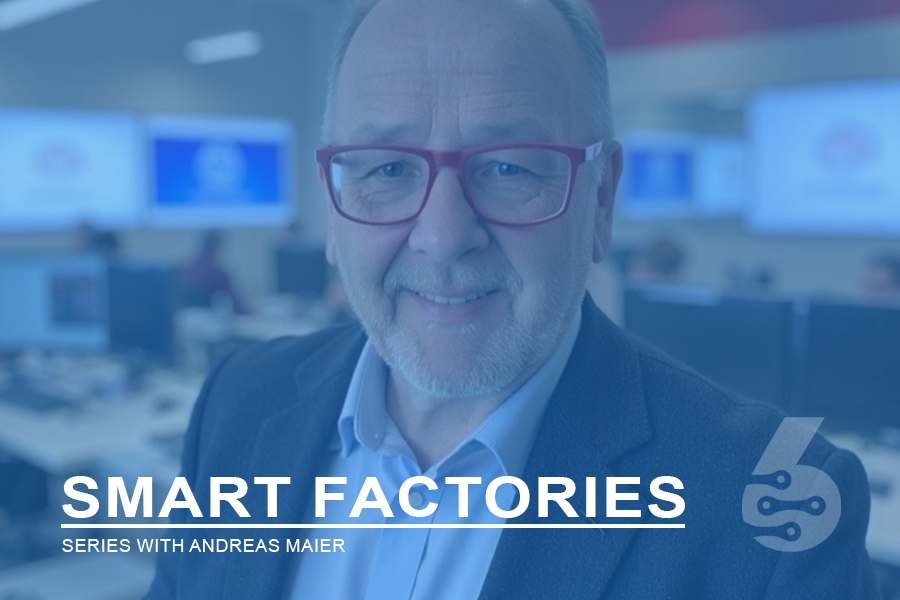
Smart Factories for Smart Snacks: How SIX ERP Transforms Food Production
As the CEO and mastermind behind our ERP implementations, I’ve seen firsthand how manufacturing is evolving. It’s no longer just about efficiency - it’s about intelligence, adaptability, and staying ahead...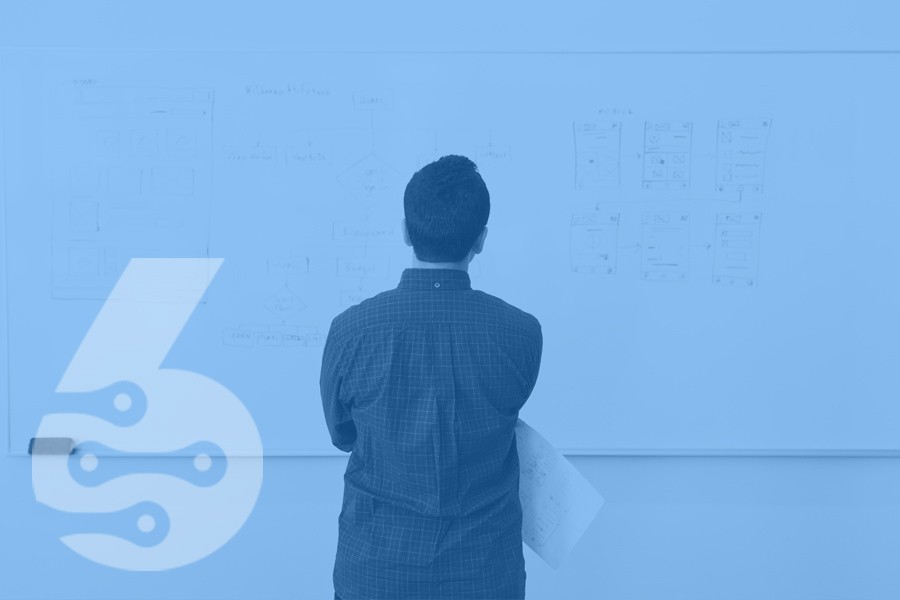
ERP Acquisition: How to Prepare an RFQ to Buy the Right ERP Solution
When your business grows, and you realize that you need an ERP solution, the next step is to start thinking about acquiring it. One of the first steps in this...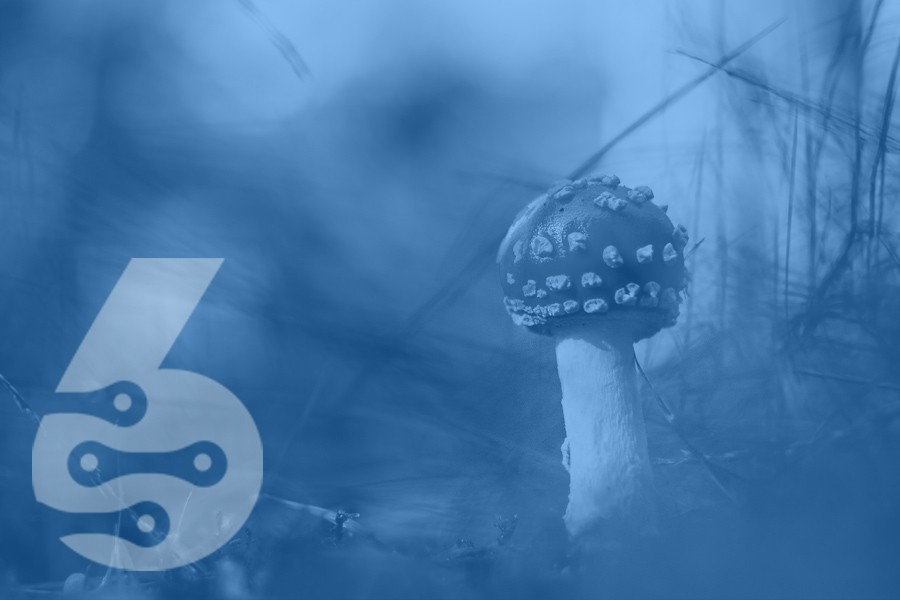