- WHMS
- 29.03.2024
Warehouse management systems (WMS) explained – Managing modern businesses.
The ins – and outs to a modern warehouse management solution
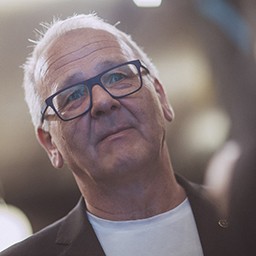
Dr. Andreas Maier
29.03.2024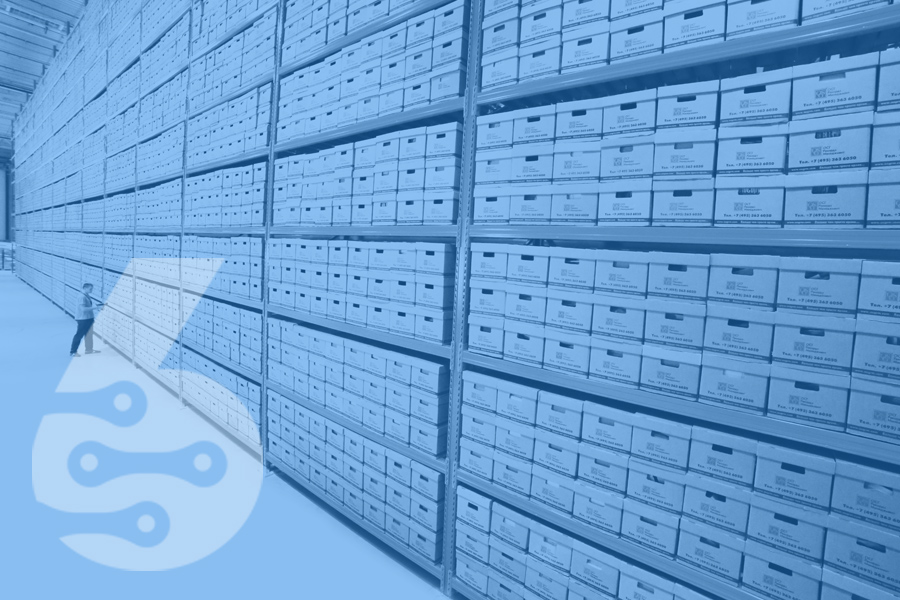
Warehouse operations are at the heart of many businesses, enabling the smooth and efficient flow of goods to customers. However, managing inventory, orders, shipping, and personnel in one or more warehouses is an enormously complex undertaking. Errors and inefficiencies in warehouse management can lead to product shortages, delayed shipments, and deteriorating customer service.
At this point, a robust warehouse management system (WMS) is essential. A WMS is software that helps control and optimize all key activities in a warehouse and distribution centre. From inventory tracking to order fulfilment and personnel management to integration with other backend systems, a WMS enables companies to deliver the right products to the right customers at the right time.
Core functions of a warehouse management system
Inventory Management
One of the fundamental functions of a WMS is real-time visibility and management of inventory throughout the warehouse. As shipments arrive at or leave the warehouse, the WMS automatically updates inventory quantities and locations. This ensures high accuracy of inventory data and minimizes the occurrence of product loss or inventory discrepancies.
By accurately counting inventory and optimizing warehouse locations based on speed and dimensions, companies can significantly improve inventory turns and reduce warehouse costs. A WMS also enables effective cycle counting workflows for routine inventory verification.
Order Management
At its core, the warehouse's job is to fulfil customer orders accurately and on time. A WMS is essential to efficiently manage the order picking, sorting, packing and shipping processes.
When customer orders arrive, the system can determine optimal picking routes based on product locations and picker availability. Pickers are guided through the warehouse with instructions displayed on mobile devices. The WMS tracks items as they are picked, ensuring that the correct items are delivered.
Packing instructions can be given based on shipping method and destination to optimize the use of containers and pallets. Finally, the WMS facilitates the creation of labels, manifests and shipping documents needed to ship orders.
Automating and streamlining these fulfilment processes improves order accuracy, increases productivity, and provides real-time visibility into order status.
Inbound and outbound operations
Managing inbound and outbound warehouse operations is another key function of a WMS. In inbound processing, the system manages the receipt and put away of products coming from distributors and suppliers. This includes scheduling loading appointments, routing products to optimal storage bins based on dimensions and speed, and registering the receipt of items in inventory.
The WMS also streamlines outbound operations. It schedules the waves of order fulfilment and the labor required to meet shipping deadlines. Scheduling for carriers, integration with loading docks and shipping software, and automation of documentation improve the efficiency of the shipping process.
Data collection, reporting and analysis
A WMS depends on real-time data collection to provide visibility and inform decisions. Handheld RF devices and wireless sensors capture information about inventory movements and warehouse tasks. This data is passed to the WMS for processing.
Robust reporting and analytics help warehouse managers identify trends, optimize operations, and improve forecasting. Key performance indicators such as labour productivity, slot accuracy, and inventory turnover can be measured and tracked. Data visualization provides insights that both warehouse staff and management can make insights-driven decisions.
Human Resource Management
Optimizing human resources and roles is essential for efficient warehouse operations. A WMS provides dedicated support for personnel management across the distribution centre.
Task management assigns activities to individual warehouse areas based on staff priority and qualifications. Rule-based workflows determine the best sequence of tasks to minimize travel and effort. Real-time visibility of staff status and locations enables dynamic adjustments in workload distribution.
Performance monitoring tracks key metrics on individual and team productivity. This allows low-performing areas to be addressed with additional training or resources. A WMS also helps document processes and procedures to efficiently onboard new employees.
The business benefits of using a robust WMS are many, ranging from tangible cost reductions to improved customer service. Below are some of the key benefits that businesses can take advantage of.
Benefits of using WMS systems
With a WMS that tracks inventory quantities and locations in real time, inventory accuracy improves dramatically compared to manual processes. Companies get a complete view of what products they have in stock and where they are in the warehouse. Inventory discrepancies and losses are minimized, as are the associated costs.
Increases labour productivity
Automating and streamlining workflows through a WMS ensures that workers spend their time on productive tasks, not administrative tasks. Routes are shortened as the system assigns tasks based on efficient pick paths and proximity to staff. Improvements in inventory allocation also improve picking efficiency over time.
Enables higher volume with existing infrastructure.
With a WMS, companies can handle higher order volume and warehouse throughput without expanding their infrastructure. Better use of existing warehouse space and employee hours leads to higher capacity. Intelligent delegation of tasks prevents bottlenecks. This provides scalability to handle business growth over time.
Reduces operating costs
Increasing productivity and efficiency in the warehouse results in significant cost reductions. Labor, inventory management, and order error costs decrease dramatically. The system also helps identify and eliminate waste in processes. When you achieve these improvements without expanding infrastructure, operating costs decrease as a percentage of sales.
Improves customer satisfaction
Thanks to streamlined fulfilment processes and near-perfect order accuracy, customers receive the right items on time and without errors. Shipping errors and damaged goods are minimized. Real-time order tracking further enhances the customer experience. This leads to higher customer retention and satisfaction.
Improves supply chain integration
A WMS serves as a central platform for visibility across the supply chain. Integration with suppliers provides visibility into order status and upcoming replenishment. Connecting with transportation partners enables shipping and logistics collaboration. This end-to-end integration facilitates responsive order fulfilment.
Provides actionable insights
The data analytics capabilities of a WMS enable managers to make smarter decisions about warehouse operations. Key metrics on employee productivity, warehouse utilization, order cycle times and inventory turnover can be monitored. Trends are analysed to identify problems and opportunities for improvement.
Drive automation initiatives
A WMS provides the basic infrastructure to enable automation of certain warehouse functions. Inventory tracking and orchestration of order fulfilment workflows enable the integration of automated picking, sorting, and conveying systems. This sets the stage for cost-effective automation.
SIX ERP – Where Every Click Moves Your Business Forward.
Choosing the right WMS
Given the wide variety of WMS solutions on the market, selecting the right software is both an important and difficult task. Each company's needs are unique due to factors such as industry, distribution model, geographic location and more. However, there are some best practices that can help with the evaluation:
- Define functional requirements that go beyond basic functions. Will advanced wave scheduling or loading scheduling provide significant benefits?
- Assess integration needs with surrounding supply chain systems to avoid future gaps in visibility.
- Determine if workflows or reports need to be customized for your environment.
- Review on-premise or cloud deployment options and associated infrastructure needs.
- Check to see if the vendor is willing to continually invest in improving and innovating the solution.
- Find out about the implementation timeline, resources required, and availability of post-implementation support.
- Talk to customers who are already using the system to verify ease of use, flexibility and scalability.
Given the wide variety of WMS solutions on the market, selecting the right software is both an important and difficult task. Each company's needs are unique due to factors such as industry, distribution model, geographic location and more. However, there are some best practices that can help with the evaluation:
- Define functional requirements that go beyond basic functions. Will advanced wave scheduling or loading scheduling provide significant benefits?
- Assess integration needs with surrounding supply chain systems to avoid future gaps in visibility.
- Determine if workflows or reports need to be customized for your environment.
- Review on-premise or cloud deployment options and associated infrastructure needs.
- Check to see if the vendor is willing to continually invest in improving and innovating the solution.
- Find out about the implementation timeline, resources required, and availability of post-implementation support.
- Talk to customers who are already using the system to verify ease of use, flexibility and scalability.
Taking the time up front to thoroughly review options and align with long-term business needs will help you avoid costly implementation pitfalls later.
Implement a future-proof system
The market for WMS solutions is constantly evolving as new technological innovations continue to emerge. When evaluating systems, it's wise to invest in a platform that will grow with the times and not become obsolete.
Key technological advancements to evaluate include:
- IoT integration for real-time visibility of inventory and equipment.
- AI-powered capabilities such as predictive demand forecasting
- Integration of advanced automation and robotics
- Augmented reality to control warehouse operations
Further supply chain visibility through blockchain integration
By choosing a solution with a solid roadmap for integrating cutting-edge technologies, companies can avoid having to replace their systems as innovations emerge.
Conclusion
As customer expectations for speed and accuracy increase, warehouse management is more important than ever to the success of companies with distribution networks. However, without a powerful WMS, it is impossible to maximize the efficiency of complex warehouse operations. This technology integration provides end-to-end visibility, cost reductions, and responsive customer service. For companies looking to gain a competitive advantage through distribution and supply chain excellence, deploying a robust warehouse management system is no longer an option, but an absolute necessity.
About the author
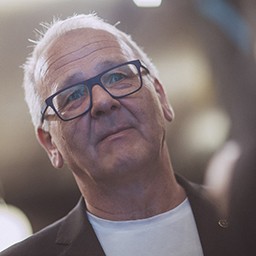
Andreas Maier is a results-driven CEO with nearly 30 years of experience in ERP, digital transformation, and IT consulting. He has held leadership positions in Fortune 100 companies such as rentalcars.com (PCLN) and Intrasoft International, a leading EU-based R&D software vendor. With a Ph.D. in Neural Networks from the University of Cologne, Andreas combines deep technical expertise with a strategic approach to business process optimization.
As the founder and co-founder of multiple successful startups, including XXL Cloud Inc., eShopLeasing Ltd, and WDS Consulting SA, his expertise lies in ERP consulting, IT strategy, and process automation. His work is focused on helping businesses implement scalable ERP solutions, streamline operations, and drive digital transformation.
Related articles
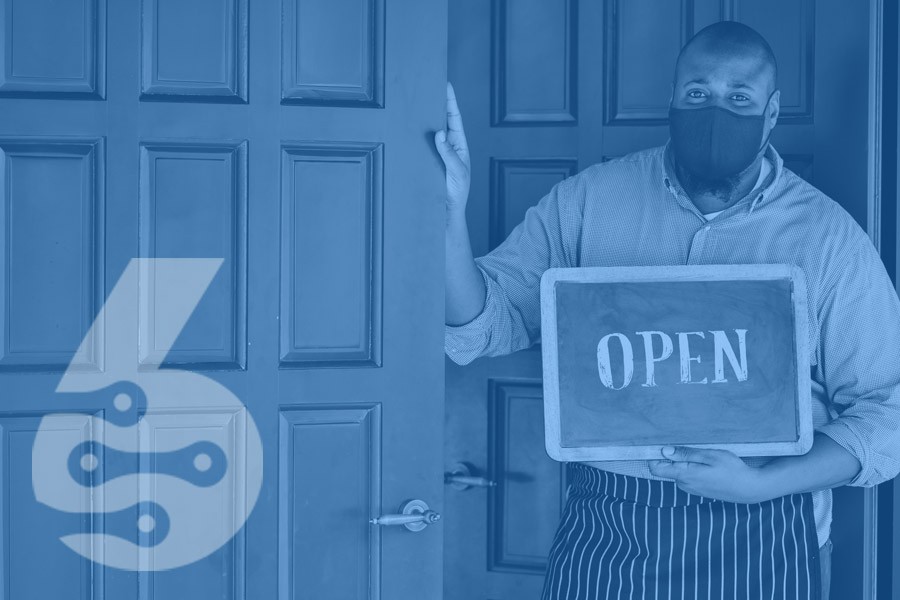
10 key features SMEs should look for in a modern ERP software
SMEs are the backbone of the economy. SMEs account for 99.7% of businesses in regions like Europe and the U.S. and employ over 60% of the workforce. But even though...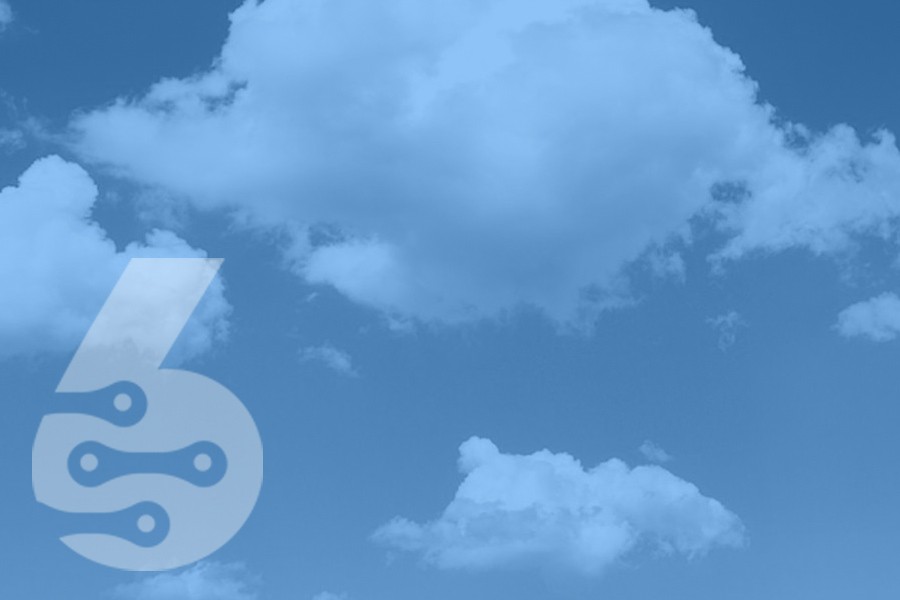
Managed Cloud ERP
As your business grows, it becomes increasingly important to have a reliable and efficient system to manage your operations. A cloud-based ERP system is the perfect solution for businesses of...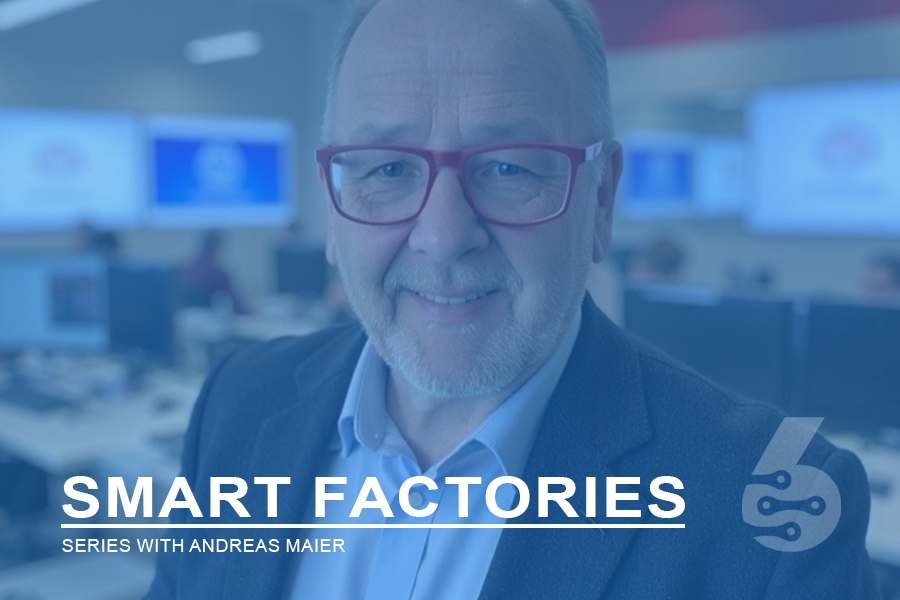