Safety stock is a reserved amount of materials that are not typically needed but is held in case of unexpected circumstances. This allows organizations to maintain a certain level of product availability and avoid disruptions in the event of an unexpected increase in demand or decrease in supply.
Organizations must carefully balance their safety stock levels to avoid stockouts and excessive inventory levels. Maintaining too little safety stock can result in lost sales and unhappy customers while carrying too much safety stock ties up capital and increases storage costs.
Organizations must consider factors such as lead time, demand variability, and supplier reliability to determine the optimal level of safety stock. An experienced inventory management team can help you strike the right balance for your business.
Related Blog Articles
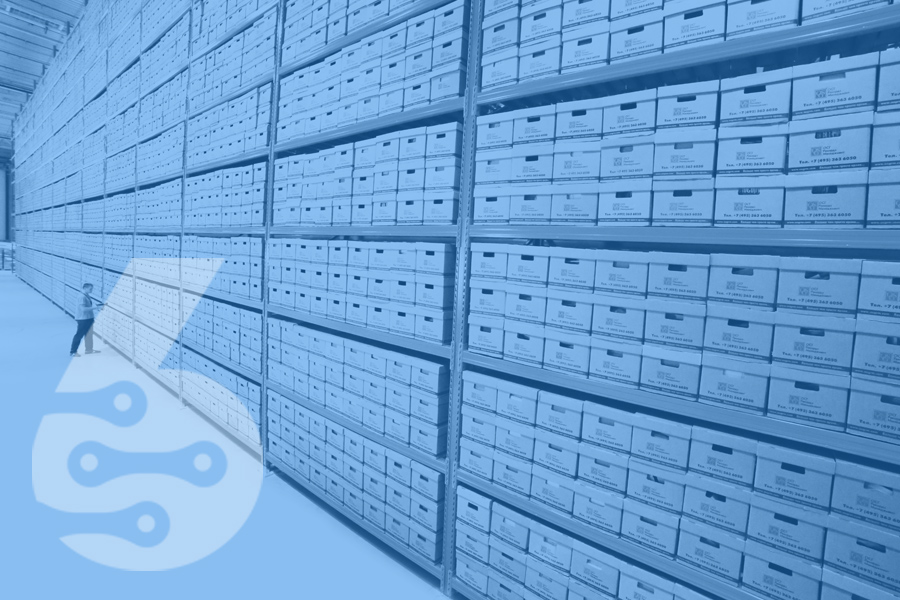
Warehouse management systems (WMS) explained – Managing modern businesses.
Warehouse operations are at the heart of many businesses, enabling the smooth and efficient flow of goods to customers. However, managing inventory, orders, shipping, and personnel in one or more warehouses is an enormously complex undertaking. Errors and inefficiencies in warehouse management can lead to product shortages, delayed shipments, and deteriorating customer service. At this point, a robust warehouse management system (WMS) is essential. A WMS is software that helps control...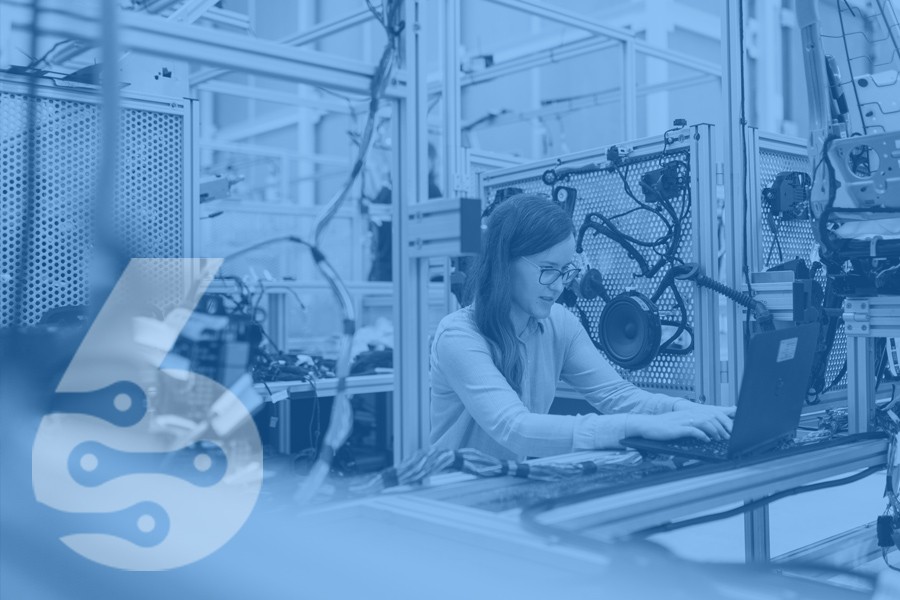
Implementing ERPs in manufacturing companies - Tips and Considerations
Are you considering implementing an ERP in your manufacturing company? It's a big decision, and there's much to consider. But don't worry - we're here to help. This blog post will share tips and tricks for making the most of your ERP implementation. Whether you're just starting or you've been working with ERPs for years, we hope you'll find these tips helpful. So let's get started!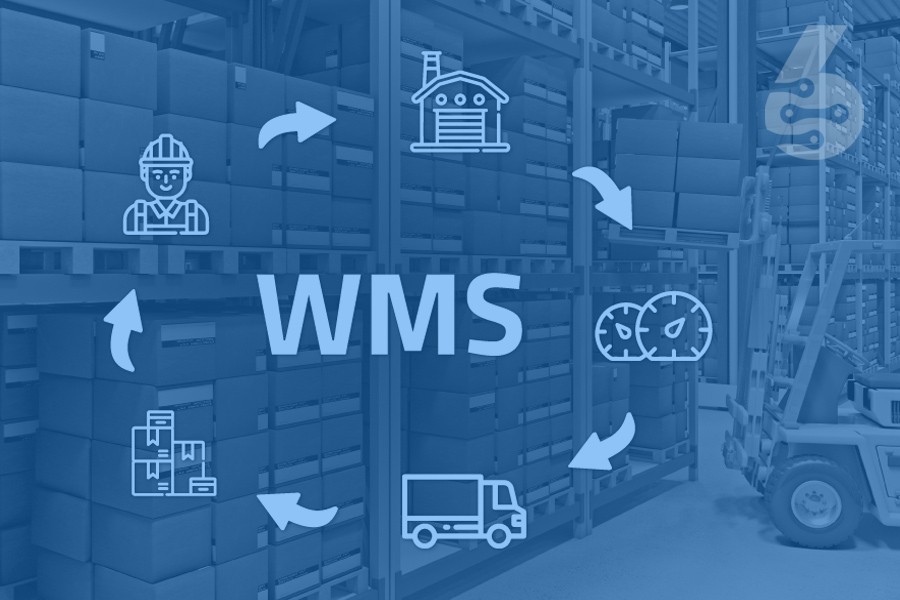
Understanding Warehouse Management Solutions
A warehouse management system (WMS) is a software application that supports the day-to-day operations in a warehouse. A WMS helps to control and direct the movement of materials within a warehouse and plays an essential role in optimizing the efficiency of these operations. There are many things to consider when implementing a WMS, from the size and layout of your warehouse to the type of products you're storing. This blog...Related SIX ERP Solutions:
Want to see SIX for yourself?
Need help, have questions or want to get a free demo?
Please read our Privacy Policy on how we process personal data. We will never share your data!